THE seriousness of first national car company PROTON grappling with severe spare parts shortage for accident repairs and scheduled servicing is so critical that it warrants the intervention of CEO Dr Li Chunrong himself.
As revealed by leading automotive site paultan.org, Dr Li – the first non-Malaysian CEO who has been helming PROTON since September 2017 – has personally been leading the after-sales battle with a ‘war room’ strategy.
Doubtlessly, PROTON is well-aware that unhappiness among its customers has reached a boiling point which if left unchecked, “might chip away at sales (not happening yet, bookings are still strong) and cause permanent damage to its reputation”.
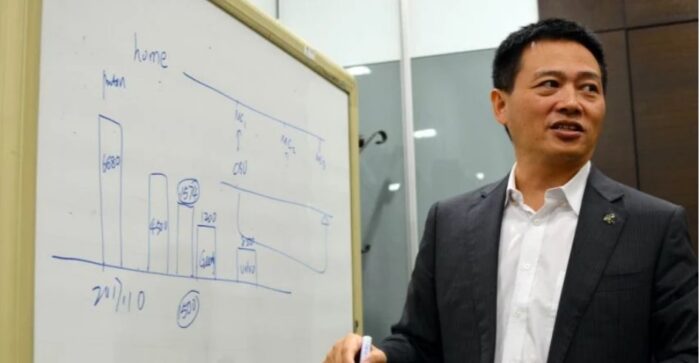
Nevertheless, the tell-tale signs are there as CGS-CIMB Research has highlighted in its latest automotive sector review that Proton’s sales volume fell by 24.3% year-on-year (yoy) in the first two months of this year (2M 2022) mainly due to its weaker sales in January.
Recall that both Perodua’s and Proton’s operations were affected by parts shortages as their vendors’ and suppliers’ operations were temporarily halted by incident of floods in late December last year. Therefore, the national segment’s market share fell by 9.3% pts yoy from 66.5% in 2M 2021 to 57.2% in 2M 2022.
Nevertheless, Proton’s sales volume has rebounded by 2.1 times month-on-month (mom) to 9,039 units in February (vs 4,316 units the previous month).
“We take it seriously on finding what’s the root cause, what makes these customers unhappy, and what makes the customers not get the parts on time,” Proton deputy CEO-cum-Proton Edar Sdn Bhd’s chief Roslan Abdullah told paultan.org.
“We take it seriously, not just at the level of operations, but including myself as well as Dr Li. Currently DrC Li actually chairs a meeting on a weekly basis, what we call a ‘war room’. We spend in a week minimum five hours just for after-sales. Last week, I think we spent almost 10 hours just on after-sales.”
These ‘war room’ meetings which have been happening since Jan 17 entail not just after-sales issue alone but encompass other areas such as procurement, quality and manufacturing which are not areas under Proton Edar per se.
“Just to ensure the vendors deliver the parts, and the parts from Geely come on time,” revealed Roslan.
The Geely factor is mostly associated with spare parts scarcity affecting the Proton X70 and X50 which local content usage to-date is only in the 50% region (as opposed to the Saga which boasts local content as high as 90%).
According to Roslan, firefighting takes up a fair bit of time during the ‘war room’ meeting. This centres around managing complaints that PROTON receive and what they read on social media. Beyond that, PROTON is putting in place long-term plans to ensure that the parts shortage problem is resolved.
All-in-all, PROTON expects to have adequate stock of fast moving parts by end-June. “What we define by adequate stock is three months of stock at the dealership, three months stock at our warehouse and certain amount of month stock at our vendors,” noted Roslan.
Earlier in March, Proton officially announced that all its dealers are now required to have three months holding stock for 22 different fast-moving parts. Aside from the new mandatory requirement for dealers to have three months holding stock, the same will apply to the central parts centre in the hopes of reducing waiting time for customers.
“We are aware of the issue on aftersales and parts availability as our customers have reached out to us. It is deeply regrettable and I would like to re-assure our customers that we take every complaint seriously and senior management has identified several bottlenecks and operational issues that require fixing,” added Roslan back then. – March 28, 2022
Pic credit: paultan.org